About eTrack
eTrack monitors machines & movement.
You get actionable insights to prevent downtime and protect your people.
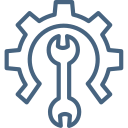
Predictive + Prescriptive Maintenance
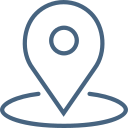
Utilization & Location Tracking
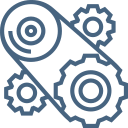
Impacts & Unstable Operations
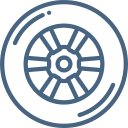
Tire and Machine Health
“eTrack was born from our passion to make the workplace work better and protect your assets: people and equipment.”
– Barbara Timm-Brock
When I was 28, my husband, 5 month old baby, and I almost died from a heavy equipment malfunction. My passion for safety was launched! As an senior operational leader in schools, foodservice, and facilities, broken equipment was a distraction for our teams. Yet maintenance technology was either too expensive and complicated to be practical, or it only worked on new equipment. Safety programs suffered from lack of visibility — we never really knew what our people and heavy equipment were doing: location or how they were operated. Even with great intentions, lack of training and unreliable maintenance created expensive downtime.
When Ed and I started eTrack, we conceived of a simple, low-cost solution to work on all ages and brands of equipment — and industrial IoT could make it real-time. We wanted simple, easy to use up to the minute dashboard that operators could use: from maintenance managers to senior executive. eTrack was born!
Memberships & Awards
Member: Arizona Tech Council
Winner: Arizona Innovation Challenge
Top 5: Tech Crunch Startup Battlefield Disrupt
eTrack’s proprietary best-in-breed sensors and software provide you with real-time insights.
eTrack applies a proprietary sensor set and communications system to your equipment using a secure, non-invasive adhesive process that keeps your warranty intact. Sensor data is transmitted to our eTrack Cloud where a proprietary business rules engine and database process your equipment and operational data, sending you real-time Alerts or posting real-time Business Intelligence to your Insight dashboards.
eTrack’s professional services team can customize your solution through high quality analytics.
Using your work orders and invoice information, we conduct a confidential proprietary analysis with personalized recommendations for your business.
This approach, driven by a set of rules and database tools, identifies issues that can be detected, issues that can be prevented, and provides recommendations for immediate actions to reduce costs or improve other operational areas.
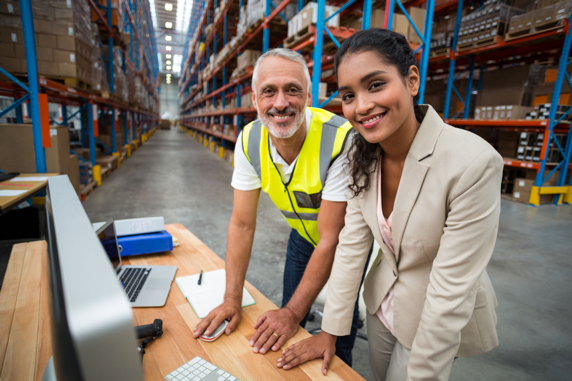
eTrack serves as a collaboration tool, providing value to finance, operations, HR and IT leadership.
What is the value of eTrack to operators?
eTrack insights enable customers to increase uptime, plan maintenance workflow before breakdowns, reduce maintenance costs by planning instead of reacting, and improve workplace safety.
What does eTrack do?
eTrack uses proprietary technology to make the invisible visible, providing actionable insights for: operations, predictive and prescriptive maintenance, equipment and operational safety, and more.
Why do this? We already get too much data and no one has time to review it.
This is not more data – you have access to your data but eTrack’s solution is not the data, but the insights that come from the data.
eTrack gives operational alerts, prescriptive instructions, and insights, versus lots of difficult to use data.
The heavy equipment manufacturers already have IoT devices on their equipment, so why would we use eTrack?
eTrack works on old and new equipment, regardless of technology level, and works on all brands of equipment, so you only need one solution to see ALL of your equipment. eTrack does not focus on machine jargon, but on providing real-time actionable information, tracking the operational and machine performance in your operations.
When you say “insights” what do you mean?
Insights include: emerging or recurring maintenance issues, actions to prevent downtime, utilization and idle time detail, equipment health, equipment geo-location, operational practices, e.g. impacts, unstable operation, and more
We already have an ERP or Workorder platform so won’t this add extra complexity?
eTrack can integrate with your existing system or your vendor’s system through APIs. The dashboards are cloud-based and intuitive, with the ability to download, analyze, or share information by any stakeholders defined by the customer.
How does eTrack help me with our workforce?
Trained operators and technicians are increasingly difficult to find and keep. eTrack Insights enable re-training and retention, improved maintenance planning, and ultimately provide a workplace with safer people and operational practices.
We use an outside vendor for our equipment (rent) or for our equipment service. How can eTrack help us?
Are you renting the right amount or type of equipment for your operation? Was that recent non-warranty repair really “abuse” or was it really an ongoing problem inherent to the equipment. Did the vendor fix the problem? Where are people working? What and when will the next breakdown occur, and how can we prevent it, and the associated productivity loss? These are questions that eTrack insights helps answer.